Here are a few photos of the fracture surface of the axle on my '48 Deluxe Sedan. The part has been reviewed by a material engineer that is familiar with fracture analysis. The conclusion was multi-origin crack initiation followed by fatigue. The peculiar marks are indicative that the individual cracks were not on the same plane at initiation, but combined during the fatigue process.
I belong to a local Model A Ford club . . . the Model A shares a similar rear axle design. The wisdom from the members that are 'mechanically inclined' suggest that a re-torqueing of the axle nut is required after some 100 miles, or the likelihood of an axle failure becomes a distinct possibility.
When it came time to torque the axle nut I started with the minimum suggested torque and applied that amount. The taper was clean and dry, while the thread and washer faces were lubed with engine oil. I used a new key that had been pre-fitted on both the axle and hub. Quite by chance there was alignment of the cotter pin hole and castellation at the minimum torque. I also tapped the hub radially with a ballpeen after torqueing . . . not a lot, and nothing severe. The torque remained the same after this tapping exercise.
After almost 200 miles of use a re-check of the torque revealed that the axle nut torque had significantly relaxed. Again while applying the minimum torque the nut advanced almost a full wrench flat. This time alignment of the cotter pin was not achieved, so I advanced the nut until alignment was achieved. The applied torque did not exceed the maximum specified.
I logged 957 miles between purchase of the car and the axle failure. I have no maintenance records prior to my purchase, so the history of repair is gone. Sadly all three of the gentlemen that may have some insight on the history have passed.
So the question is: Why does the tapered axle design need a re-checking of the torque after use? Clearly tapers are successfully used in machine tools, but in those applications the operational forces are typically forcing the taper 'together', and alignment and torque capacity are the desired characteristics. I have a theory, but no evidence, that the taper does not 'marry' along its entire length and 'hangs' prior to full lock-up. The nut torque alone does not produce enough force to push the hub passed this false position. Once returned to service there are forces sufficient to move the hub inboard past the initial obstruction. This system would be considered stiff, meaning a small amount of hub motion has a significant impact on the torque.
If the assembly is allowed to operate with the taper not fully engaged then there will be forces applied to the washer/nut to resist relative motion between the axle and hub. Those forces will result in a bending moment applied to the thread area of the axle . . . specifically the area of the fillet radius between the taper and thread. This area would be known as an abrupt geometry change and would carry a penalty on maximum allowed bending moment. Equally the surface finish of that radius is such that an additional penalty would be applied if the loading was cyclic.
Just an opinion/unproven theory, but I'm thinking that not all hubs and tapers 'marry' along their full length (the original design intent) and the nut becomes an unintentional load path to resist relative motion. I'm not keen on the idea of over-torqueing the nut to seat the taper and then back-off to the specified range. I don't know of any service advice about re-checking the nut torque after use . . . seems like tribal wisdom . . . in my limited experience the advice to re-torque seems well founded.
dp
Attach file:
(137.75 KB)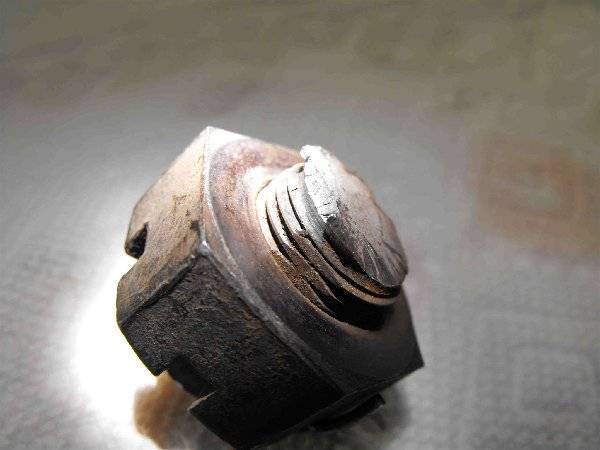
(162.13 KB)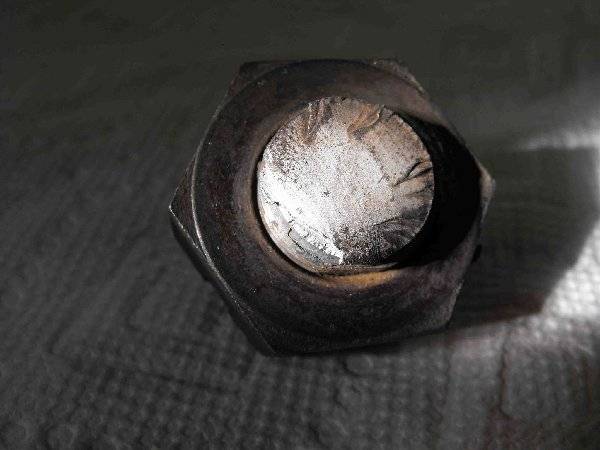
This Post was from: https://packardinfo.com/xoops/html/modules/newbb/viewtopic.php?post_id=202013